A CO2 sensor, also known as a carbon dioxide sensor, is a device designed to measure and monitor the concentration of carbon dioxide gas in the surrounding environment.
What is a CO2 Sensor?
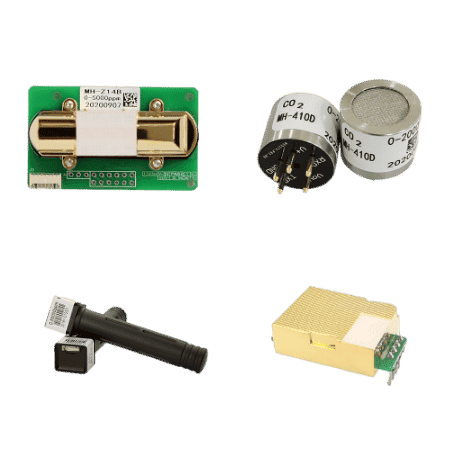
How do CO2 sensors work?
There are several different ways to measure CO2 levels, and each type of sensor uses a different measurement principle. The most common types of CO2 sensors are:
NDIR (Non-Dispersive Infrared) sensors
NDIR CO2 sensors utilize the absorption properties of infrared radiation to measure CO2 concentration. These sensors consist of an infrared light source (typically an infrared bulb), an optical chamber, and an infrared detector. The light source emits infrared radiation at a specific wavelength, which passes through the optical chamber. When the light passes through the chamber, CO2 molecules absorb specific wavelengths of the infrared light. An infrared detector measures the intensity of the light that passes through the chamber, and based on the absorption of CO2 at specific wavelengths, calculates and outputs the CO2 concentration.
Thermal Conductor sensors
Thermal conductor CO2 sensors measure CO2 concentration based on the relationship between CO2 gas's thermal conductivity and its concentration. The sensor includes a thermocouple or a thermal resistor, with one part heated and maintained at a constant temperature, and another part serving as a reference temperature. When CO2 gas flows through the sensor, it carries away heat from the heated part, resulting in a temperature difference. The sensor measures this temperature difference and converts it into a CO2 concentration reading.
Semiconductor Sensor
Semiconductor CO2 sensors utilize the electrical characteristics of oxide semiconductor materials to measure CO2 concentration. These sensors often employ metal oxide gas-sensitive materials like tin dioxide (SnO2). When CO2 gas comes into contact with the oxide material, a chemical reaction occurs at the material's surface, causing a change in its electrical resistance. This resistance change is proportional to the CO2 concentration, and the sensor measures this resistance change to determine the CO2 concentration.
There are several types of CO2 sensors available, but the most common ones are based on non-dispersive infrared (NDIR) technology.
NDIR (Non-Dispersive Infrared) sensors
Due to the different internal structures of the molecules of various substances, their selective absorption of light of different wavelengths is also different, that is to say: substances can only absorb light of specific wavelengths, and the absorption relationship of substances for light of a certain wavelength obeys the Lambert-Beer ( Lambert-Beer) absorption law.

For infrared carbon dioxide sensors, the infrared light source emits infrared light of 1-20 μm, which is absorbed by a gas chamber of a certain length, and then passes through a narrow-band filter with a wavelength of 4.26 μm, and is monitored by an infrared detector that transmits infrared light of a wavelength of 4.26 μm. The intensity of light indicates the concentration of CO2 gas.
Here's how NDIR sensors work:
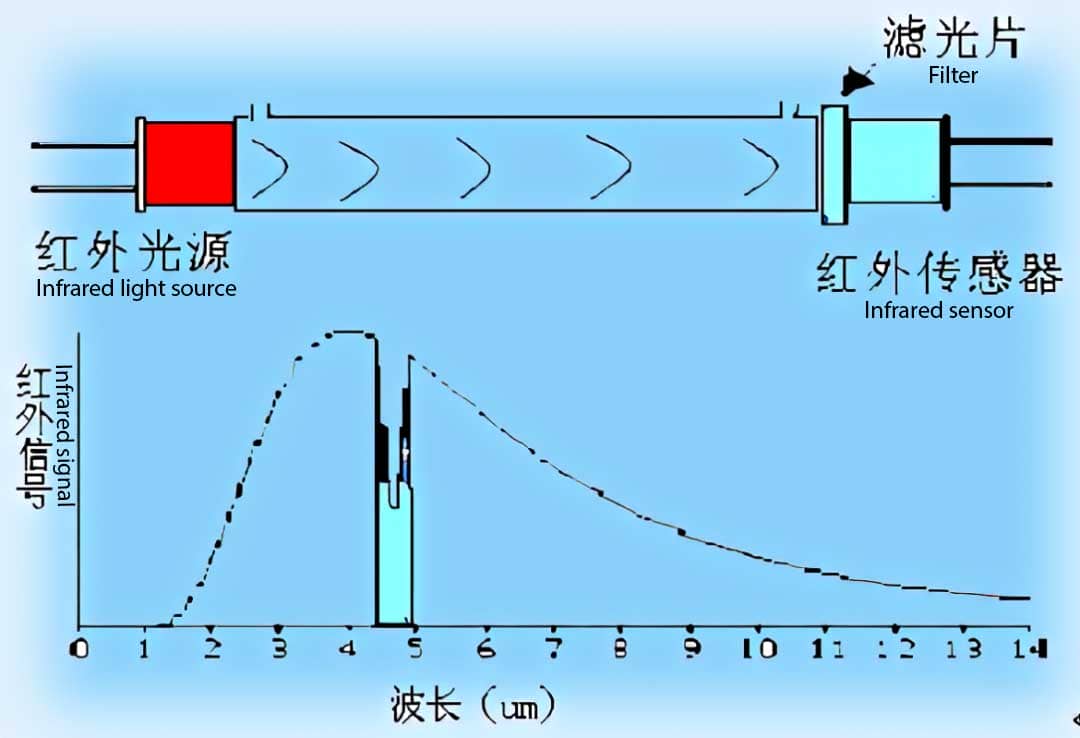
Infrared Source: The NDIR sensor consists of an infrared light source, typically an infrared bulb or LED. The source emits infrared light at a specific wavelength that corresponds to the absorption band of the gas being measured, in this case, CO2.
Optical Chamber: The sensor contains an optical chamber or cell that allows the infrared light to pass through. The chamber is designed to ensure that the gas sample being measured interacts effectively with the infrared light. Gas Sample Interaction: The air sample containing CO2 is introduced into the optical chamber. As the infrared light passes through the chamber, the CO2 molecules in the gas sample absorb the infrared light at the specific wavelength matching their absorption band.
Detector: On the other side of the optical chamber, there is an infrared detector that measures the intensity of the infrared light that has passed through the chamber. The detector can be a photodiode, photodetector, or other types of infrared-sensitive devices.
Reference Channel: NDIR sensors often utilize a reference channel to compensate for variations in environmental conditions and ensure accurate measurements. The reference channel measures the intensity of the infrared light that has not been absorbed by the target gas, providing a baseline reference for comparison.
Signal Processing: The detector converts the intensity of the transmitted infrared light into an electrical signal. This signal is processed by the sensor's electronics, which subtracts the intensity of the reference channel from the measurement channel to isolate the absorption caused by the CO2 gas.
Calibration and Output: NDIR sensors require calibration to establish a relationship between the measured signal and the actual CO2 concentration. Once calibrated, the sensor provides an output signal, typically in the form of an analog voltage or digital signal, which corresponds to the CO2 concentration in the air.
Relationship between infrared transmittance and gas concentration is expressed by the Lambert-Beer law:
T = I / I₀ = e^(-εcd)
T represents the transmittance of the infrared light through the gas sample,
I represents the intensity of the transmitted infrared light,
I₀ represents the intensity of the incident infrared light,
ε represents the molar absorptivity or absorption coefficient of the gas,
c represents the concentration of the gas, and d represents the path length of the gas sample.
The equation is based on the Beer-Lambert Law, which describes the relationship between the transmittance of light through a medium, the concentration of the absorbing substance in the medium, and the path length of the medium.
According to the equation, the transmittance (T) is the ratio of the transmitted light intensity (I) to the incident light intensity (I₀). It is related to the concentration (c) of the gas and the path length (d) through the exponent of the term e^(-εcd).
The term εcd represents the product of the molar absorptivity (ε), which is a measure of how strongly the gas absorbs infrared light at a specific wavelength, and the concentration (c) of the gas multiplied by the path length (d) of the gas sample. This term quantifies the extent of absorption of the infrared light by the gas sample.
As the concentration or path length increases, the term εcd increases, resulting in a decrease in the transmittance (T) of the infrared light. This decrease in transmittance corresponds to a higher absorption of the light by the gas sample, indicating a higher concentration of the gas.
By measuring the transmittance of the infrared light through the gas sample and knowing the path length and molar absorptivity of the gas, the concentration of the gas can be calculated using the Beer-Lambert Law equation.
CO2 sensor application
CO2 sensors have a wide range of applications across various industries and sectors due to the importance of monitoring and controlling carbon dioxide levels. Here are some common applications of CO2 sensors:
Indoor Air Quality (IAQ) Monitoring: CO2 sensors are widely used in buildings, offices, schools, and homes to monitor indoor air quality. High levels of CO2 can indicate inadequate ventilation, which can lead to discomfort, reduced productivity, and health issues. CO2 sensors help ensure proper ventilation and enable adjustments to maintain optimal indoor air quality.
HVAC Systems: CO2 sensors are integrated into heating, ventilation, and air conditioning (HVAC) systems to optimize energy efficiency. By measuring CO2 levels, the sensors enable demand-controlled ventilation, adjusting the airflow based on occupancy and CO2 concentration to minimize energy consumption while maintaining healthy indoor environments.
Industrial Safety: In industrial settings, CO2 sensors are used to monitor and detect potentially hazardous levels of carbon dioxide. Industries such as breweries, beverage production, and chemical manufacturing utilize CO2 sensors to ensure worker safety and prevent the accumulation of dangerous levels of CO2.
Greenhouse and Agriculture: In greenhouse operations and agriculture, CO2 sensors play a crucial role in plant growth and productivity. Monitoring and controlling CO2 levels in greenhouse environments can enhance plant photosynthesis and growth, leading to improved crop yields.
Automotive: CO2 sensors are utilized in automotive applications, particularly in vehicles with internal combustion engines. They help optimize fuel efficiency and reduce emissions by providing real-time feedback on the CO2 levels in the exhaust gases, enabling engine control systems to adjust the air-fuel mixture for optimal combustion.
Environmental Monitoring: CO2 sensors are used in environmental monitoring to measure and track CO2 levels in outdoor environments. This data is essential for climate change research, studying carbon cycles, and assessing the impact of human activities on the environment.
Safety in Confined Spaces: CO2 sensors are employed in confined space monitoring to detect high levels of carbon dioxide that can pose a risk to workers. These sensors provide early warning signs and help ensure worker safety in environments such as storage tanks, tunnels, and underground spaces.
CO2 sensor hvac
CO2 sensor car/automotive
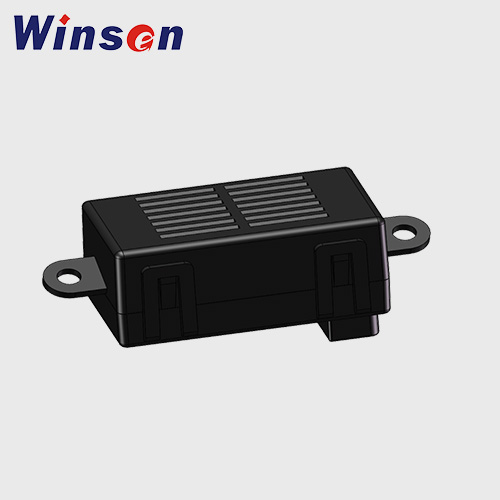
MH-V1512A NDIR CO2 Module
- CO2
- 400~10000ppm optional
- Read More
Greenhouse co2 sensor
Incubator co2 sensor
CO2 sensor price
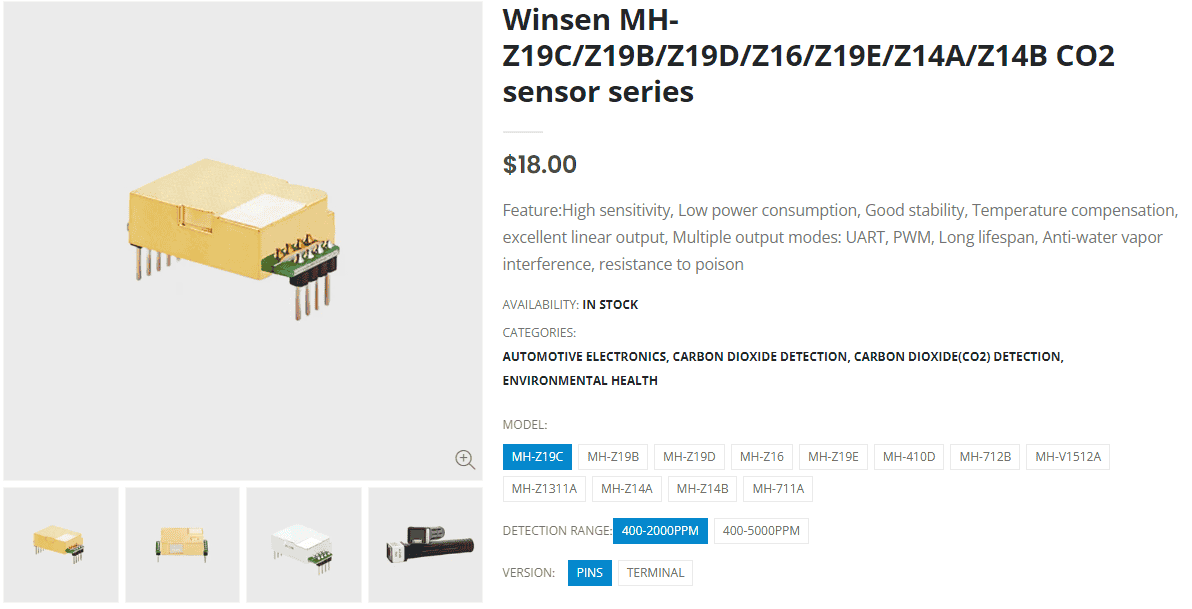
Online Shop: https://shop.winsen-sensor.com/products/winsen-co2-sensor-series?variant=43743936086208
Calibrate co2 sensor
Calibrating a CO2 sensor is essential to ensure accurate and reliable measurements. The calibration process involves comparing the sensor's readings to known reference values and adjusting the sensor's output accordingly. Here are the general steps to calibrate a CO2 sensor:
Select a Calibration Gas: Obtain a calibration gas with a known and accurate CO2 concentration. Calibration gases are typically available in pre-mixed cylinders with certified concentrations. Ensure that the calibration gas matches the range of the CO2 sensor you are calibrating.
Prepare the Calibration Environment: Set up a controlled environment that closely resembles the conditions in which the CO2 sensor will be used. This includes temperature, humidity, and pressure conditions. Stable environmental conditions are crucial for accurate calibration.
Allow for Sensor Stabilization: Power on the CO2 sensor and allow it to stabilize in the calibration environment for a sufficient period. This stabilization time helps the sensor adjust to the environmental conditions and ensures accurate readings.
Zero Calibration (Optional): Some CO2 sensors may require zero calibration, especially if they have a built-in auto-zero feature. Zero calibration is performed in a clean air environment (typically outdoor air) where the CO2 concentration is close to zero. It adjusts the sensor's baseline reading to eliminate any residual offset.
Perform Span Calibration: Span calibration involves exposing the CO2 sensor to the calibration gas with a known CO2 concentration. Ensure a proper gas delivery system is used to deliver the calibration gas to the sensor accurately. Allow the sensor to stabilize in the calibration gas environment.
Compare Readings and Adjust: Compare the sensor's readings to the known concentration of the calibration gas. If the readings deviate from the expected values, make adjustments to the sensor's output. Some sensors have calibration adjustment features, such as trim pots or software options, to modify the output accordingly.
Repeat as Needed: Depending on the sensor and calibration requirements, multiple calibration points may be necessary to achieve accurate measurements across the desired measurement range. Follow the manufacturer's guidelines for the specific number of calibration points required for your sensor.
Record Calibration Data: Document the calibration procedure, including the calibration gas concentration, calibration date, and any adjustments made to the sensor. This information is important for traceability and future reference.
Regular Calibration Maintenance: CO2 sensors may require periodic recalibration to maintain accuracy. The calibration interval depends on the sensor type, manufacturer recommendations, and the application. Follow the recommended calibration schedule and perform routine maintenance to ensure reliable measurements.
CO2 is a non-toxic gas and common. Why should we measure CO2?
The CO2 content in fresh air is 0.04%. If the CO2 content in indoor air exceeds a certain level, a certain degree of discomfort and poisoning will occur:
2.5%: No symptoms for several hours;
3.0%: The number of breathing increases unconsciously;
4.0%: local irritation symptoms occur;
6.0%: Increased respiratory volume;
8.0%: difficulty breathing;
10.0%: unconsciousness, soon leading to death;
20.0%: Paralysis occurs after a few seconds and the heart stops beating.
Concentration | PPM | Symptoms |
0.04% (Fresh air) | 400 ppm | No symptoms |
2.50% | 25,000 ppm | No symptoms for several hours |
3.00% | 30,000 ppm | Unconscious increase in breathing rate |
4.00% | 40,000 ppm | Local irritation symptoms occur |
6.00% | 60,000 ppm | Increased respiratory volume |
8.00% | 80,000 ppm | Difficulty breathing |
10.00% | 100,000 ppm | Unconsciousness, leading to death |
20.00% | 200,000 ppm | Paralysis occurs after a few seconds, heart stops beating |